The Science Behind Porosity: A Comprehensive Overview for Welders and Fabricators
Understanding the elaborate devices behind porosity in welding is critical for welders and producers aiming for impeccable workmanship. From the composition of the base materials to the ins and outs of the welding process itself, a plethora of variables conspire to either intensify or minimize the existence of porosity.
Understanding Porosity in Welding
FIRST SENTENCE:
Evaluation of porosity in welding discloses crucial understandings right into the stability and top quality of the weld joint. Porosity, characterized by the existence of cavities or spaces within the weld steel, is a common worry in welding procedures. These voids, otherwise correctly dealt with, can endanger the architectural stability and mechanical homes of the weld, leading to prospective failings in the ended up item.

To spot and measure porosity, non-destructive testing methods such as ultrasonic screening or X-ray examination are often used. These methods permit for the recognition of interior problems without compromising the integrity of the weld. By evaluating the size, form, and circulation of porosity within a weld, welders can make educated decisions to boost their welding procedures and achieve sounder weld joints.
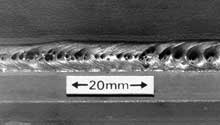
Variables Influencing Porosity Development
The incident of porosity in welding is influenced by a myriad of elements, varying from gas protecting efficiency to the intricacies of welding parameter settings. Welding parameters, including voltage, present, travel speed, and electrode kind, additionally impact porosity development. The welding strategy employed, such as gas steel arc welding (GMAW) or shielded metal arc welding (SMAW), can affect porosity development due to variants in warm distribution and gas coverage - What is Porosity.
Effects of Porosity on Weld Quality
Porosity development dramatically endangers the architectural stability and mechanical residential properties of bonded joints. When porosity is present in a weld, it creates gaps or tooth cavities within the material, reducing the overall toughness of the joint. These gaps work as anxiety concentration factors, making the weld much more vulnerable to cracking and failing under tons. The presence of porosity additionally deteriorates the weld's resistance to corrosion, as the trapped air or gases within deep spaces can react with the surrounding setting, resulting in destruction with time. Additionally, porosity can hinder the weld's capability to withstand pressure or impact, further jeopardizing the overall quality and reliability of the bonded structure. In crucial applications such as aerospace, automotive, or structural building and constructions, where safety and resilience are critical, the destructive impacts of porosity on weld high quality More Bonuses can have serious consequences, emphasizing the significance of reducing porosity via correct welding methods and procedures.
Methods to Decrease Porosity
To improve the quality of welded joints and ensure architectural stability, welders and producers read the full info here employ certain methods focused on lowering the formation of spaces and dental caries within the material throughout the welding process. One efficient method to reduce porosity is to make certain proper material prep work. This includes extensive cleansing of the base steel to eliminate any kind of contaminants such as oil, grease, or dampness that could contribute to porosity formation. Furthermore, using the suitable welding specifications, such as the right voltage, existing, and take a trip rate, is important in stopping porosity. Maintaining a regular arc length and angle during welding likewise helps in reducing the possibility of porosity.

Furthermore, picking the appropriate shielding gas and maintaining proper gas flow prices are important in minimizing porosity. Using the suitable welding method, such as back-stepping or utilizing a weaving movement, can also help disperse warmth uniformly and decrease the opportunities of porosity development. why not find out more Last but not least, making certain appropriate ventilation in the welding environment to remove any potential sources of contamination is important for accomplishing porosity-free welds. By implementing these strategies, welders can properly lessen porosity and create premium bonded joints.
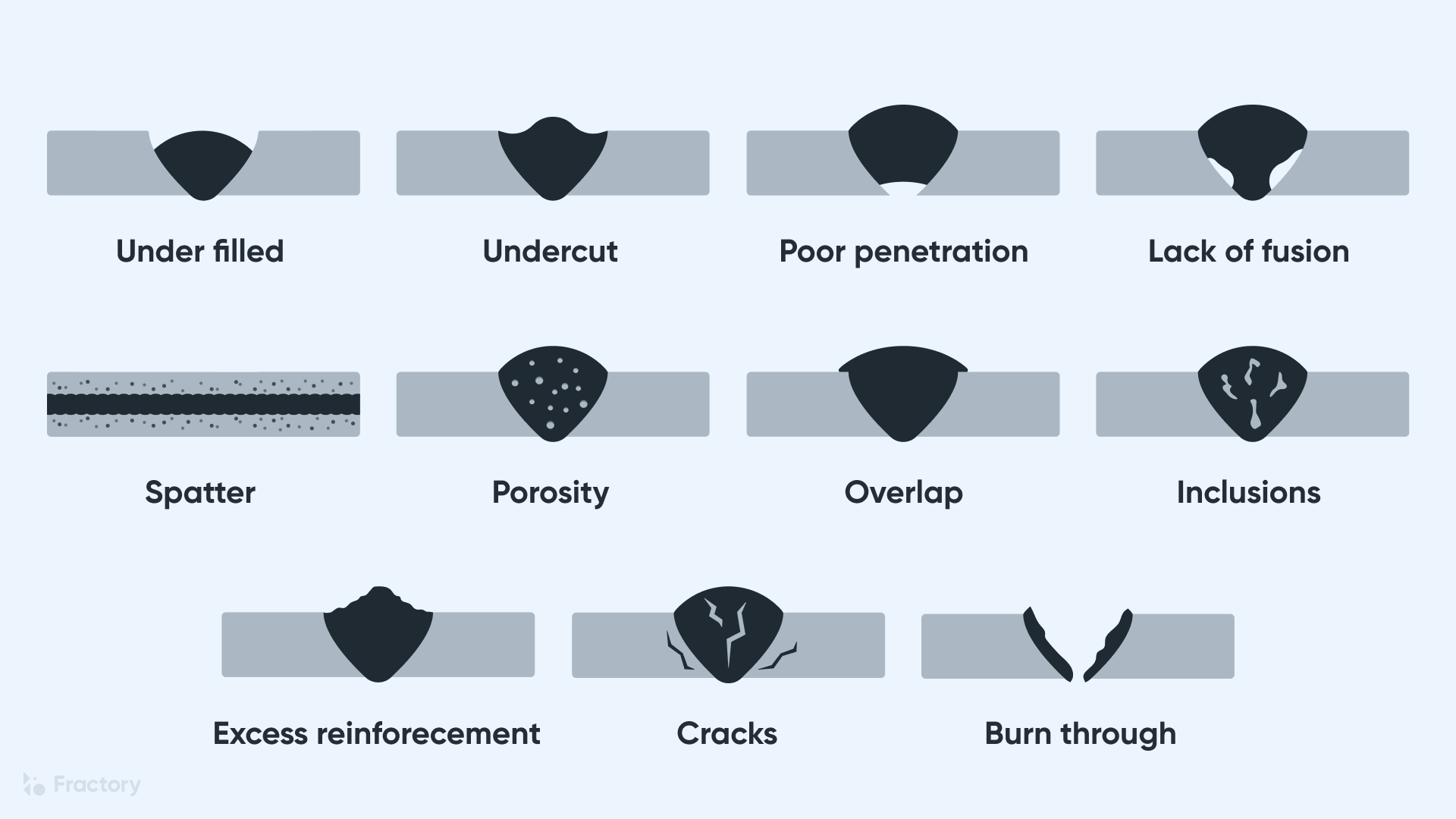
Advanced Solutions for Porosity Control
Implementing sophisticated innovations and innovative techniques plays a pivotal duty in accomplishing exceptional control over porosity in welding procedures. In addition, employing innovative welding techniques such as pulsed MIG welding or customized ambience welding can likewise help minimize porosity issues.
Another innovative solution involves making use of advanced welding equipment. For circumstances, using tools with integrated functions like waveform control and advanced power resources can enhance weld quality and lower porosity threats. The application of automated welding systems with exact control over specifications can substantially lessen porosity problems.
Moreover, incorporating innovative surveillance and examination modern technologies such as real-time X-ray imaging or automated ultrasonic screening can help in discovering porosity early in the welding process, allowing for instant restorative actions. In general, integrating these innovative options can greatly enhance porosity control and improve the total high quality of welded parts.
Final Thought
In final thought, recognizing the science behind porosity in welding is essential for welders and producers to produce high-quality welds - What is Porosity. Advanced options for porosity control can better improve the welding procedure and make certain a strong and reputable weld.